Biomedical Packaging Features
Although Heritage Packaging serves countless industries, we find that our capabilities are particularly well suited to benefit the biomedical industry. This specific field gives us a great opportunity to show off a number of finishing and fitment options for our flexible packaging products. Not a part of the bioscience or medical industries? No problem! This article will give you a great idea of the many options you have for your own packaging project.
Not a reader? Check out our comprehensive video below to learn more.
At Heritage Packaging, our team of highly skilled employees and our comprehensive array of converting equipment foster our ability to engineer cost-effective solutions to complex packaging challenges for the bioscience and medical industries.
Our flexible packaging products offer protection or preservation for customers in these industries that need products like septa pouches, high barrier hermetically sealed bags, pouches and liners; custom-shaped pouches with molded fitments installed, and a myriad of other attachments to pouches.
Through the use of the materials, processes, and custom features that we’ll explore today, we are able to offer packaging solutions for critical contents like solutions, reagents, bodily fluids, and more.
Many converters simply don’t have the equipment, experience, or processes to compete with our packaging solutions. We offer a variety of inline and secondary operations like fitment and valve installation, die-cutting, grommeting, imprinting, cleaning, kitting, and more.
Our equipment can even produce 65” long, contour sealed, in-line die cut, vision-system inspected, spouted pouches that contain medicinal powder for the pharmaceutical industry. Try saying that three times fast!
Once we know the full details of an application we help customers find the perfect configuration, material, closure method, and custom features. Join us in this video as we look closely at the different features we can add to your packaging products.
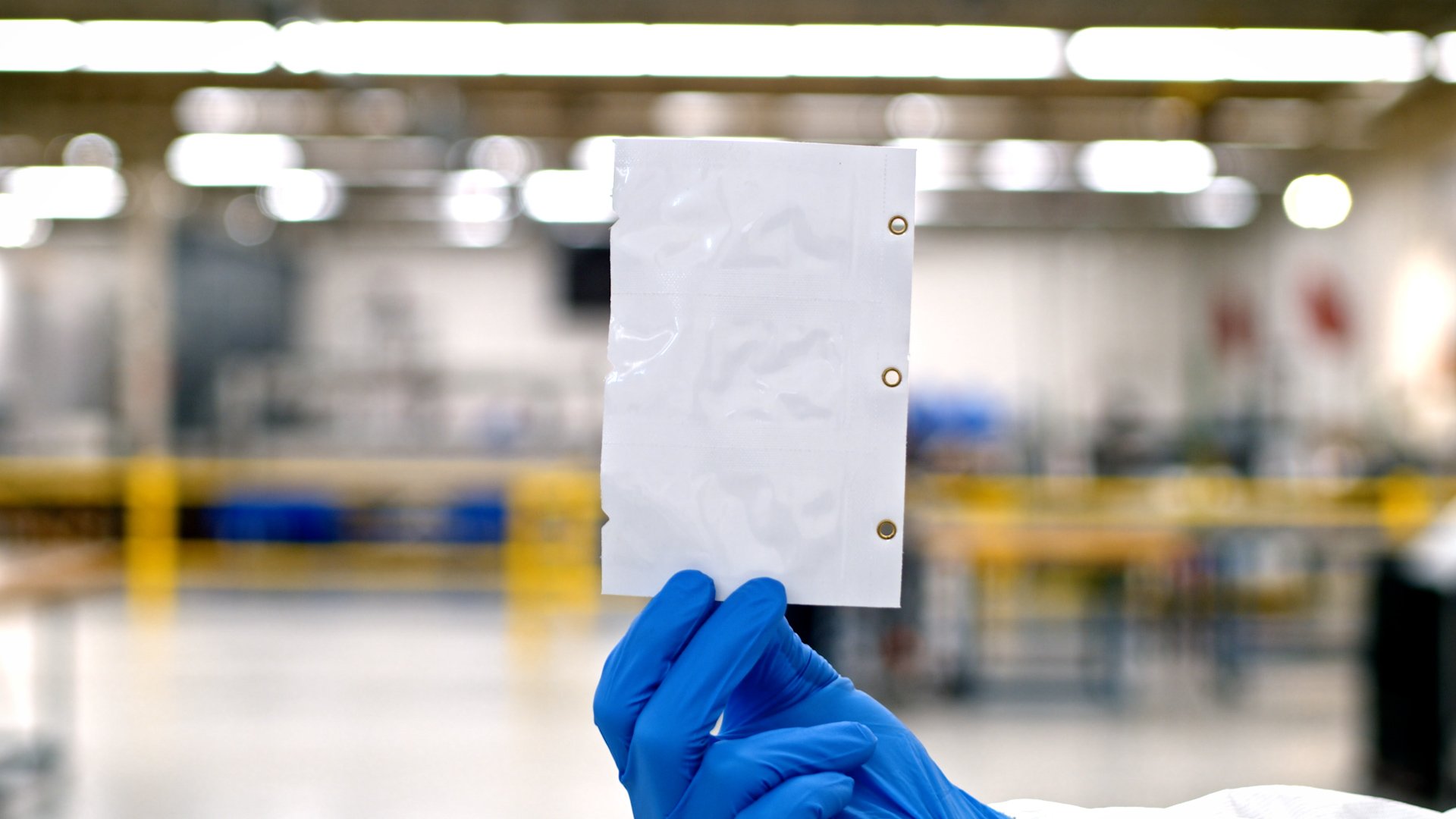
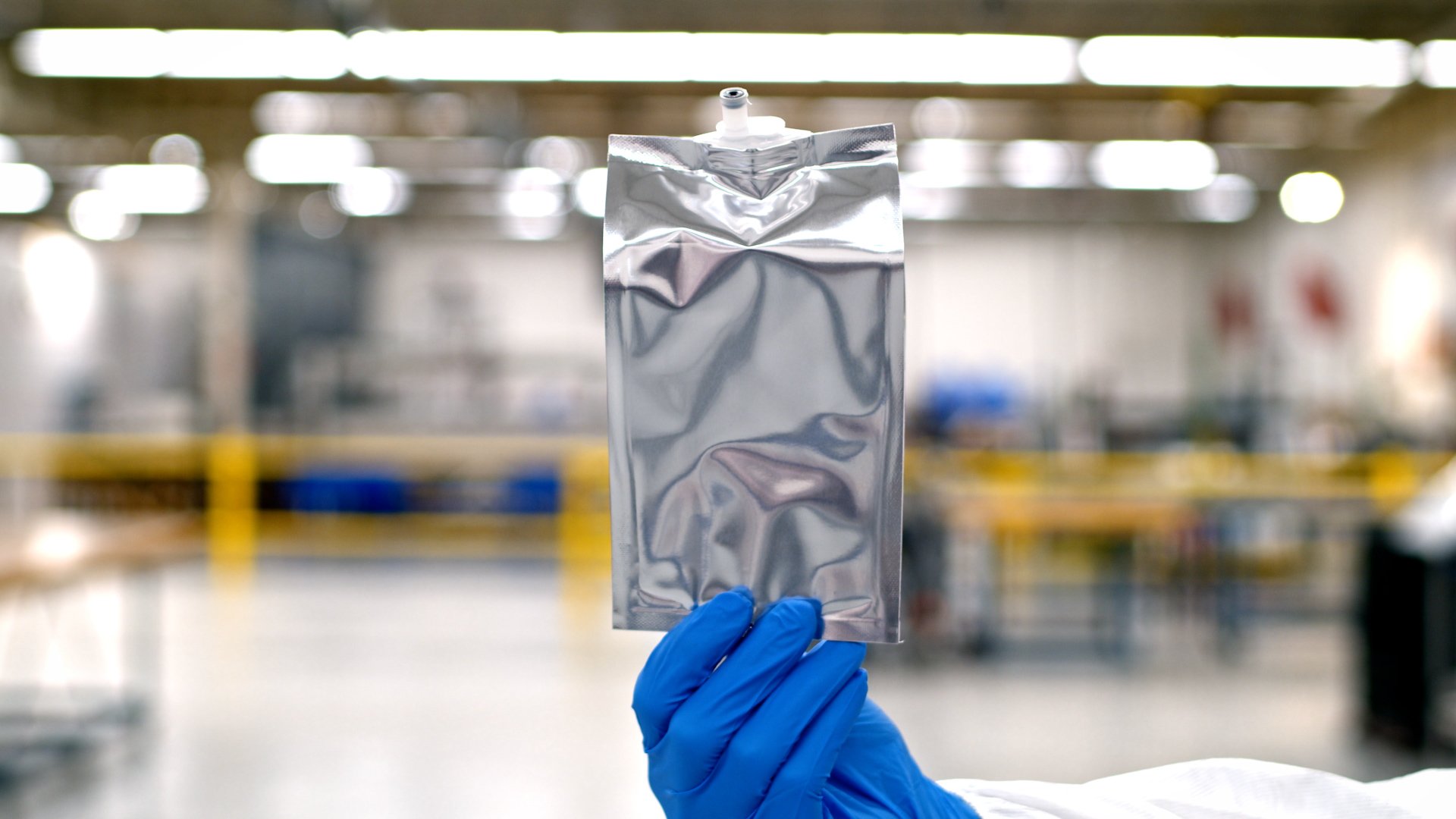
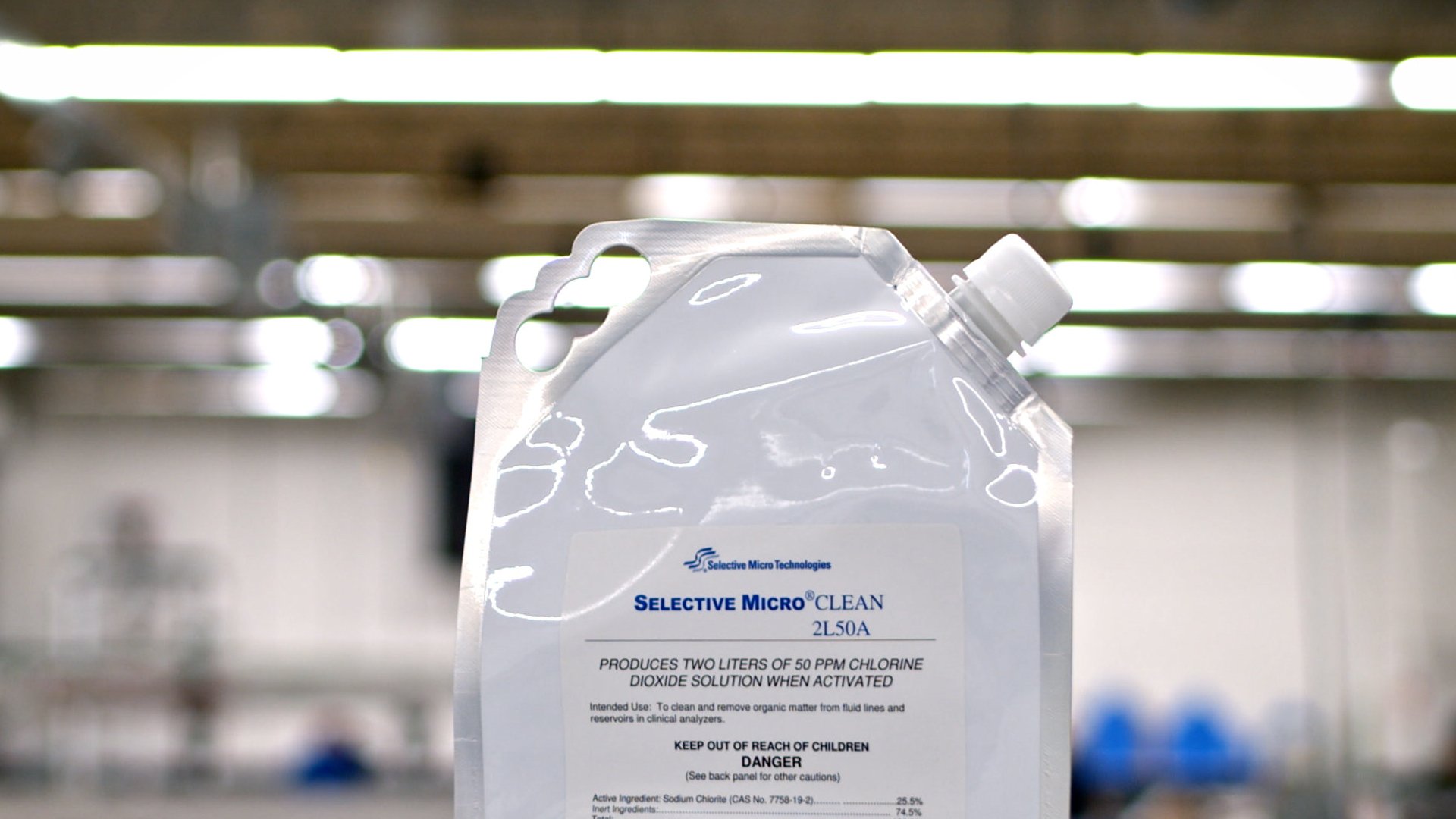
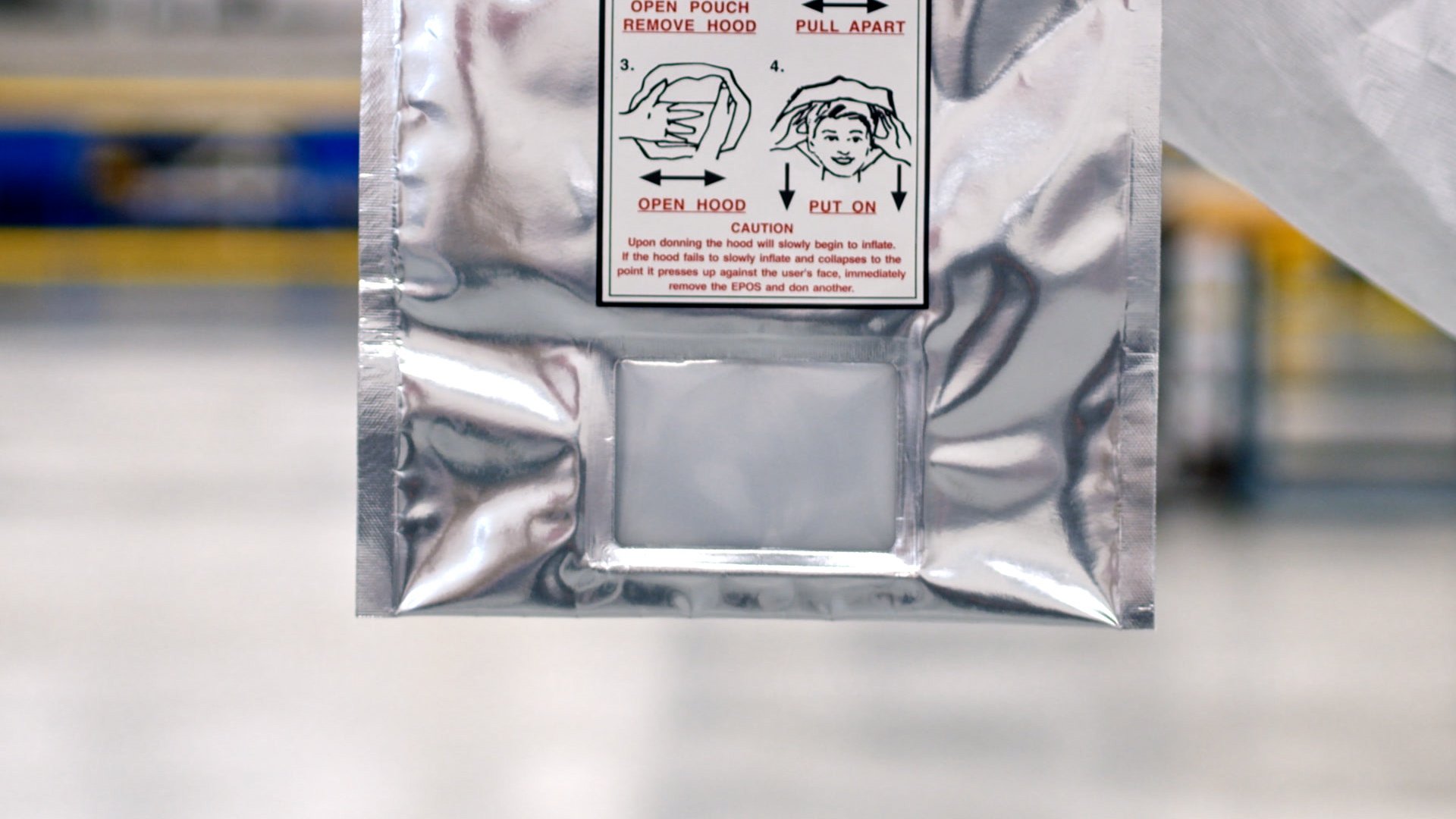
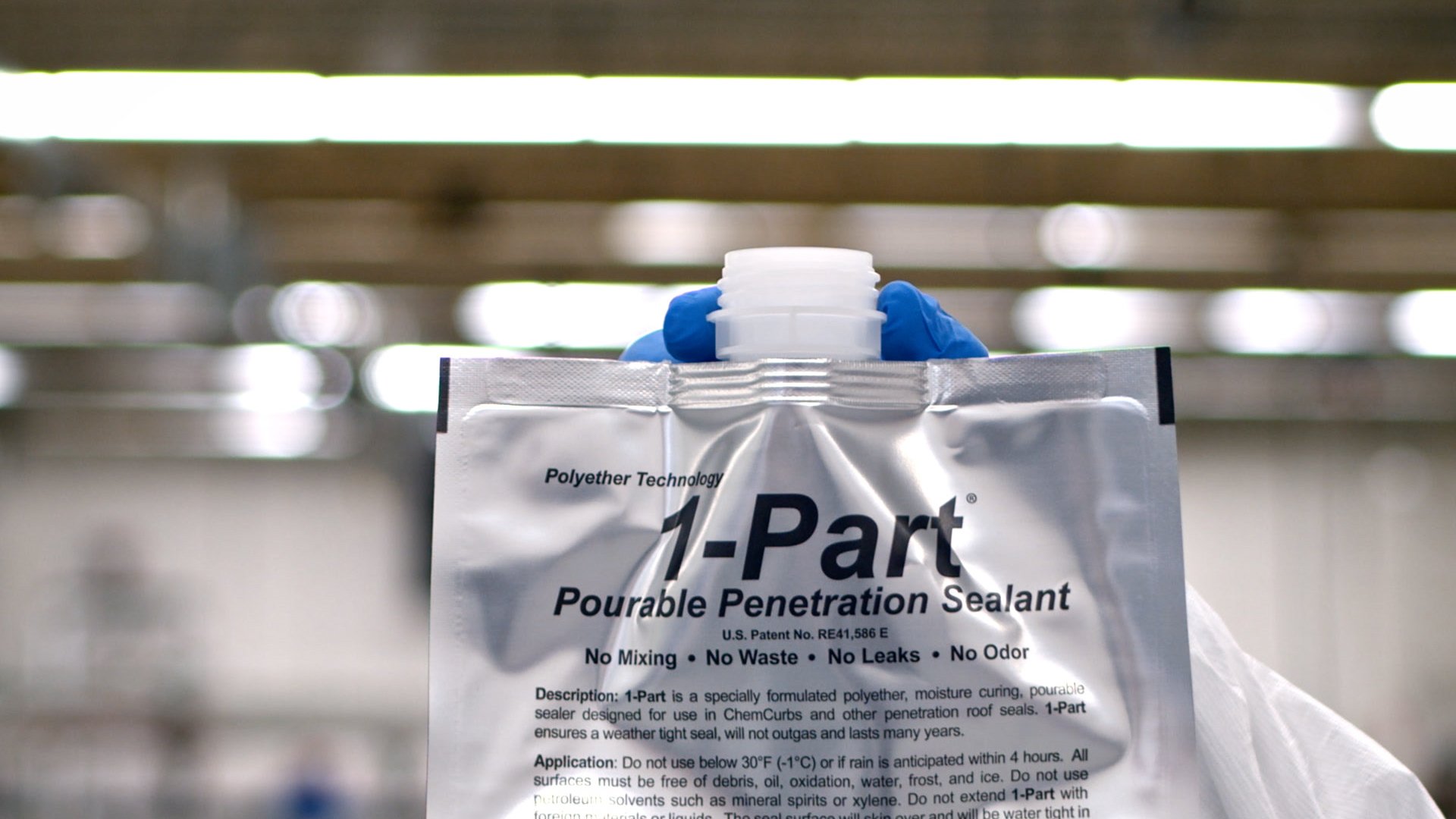
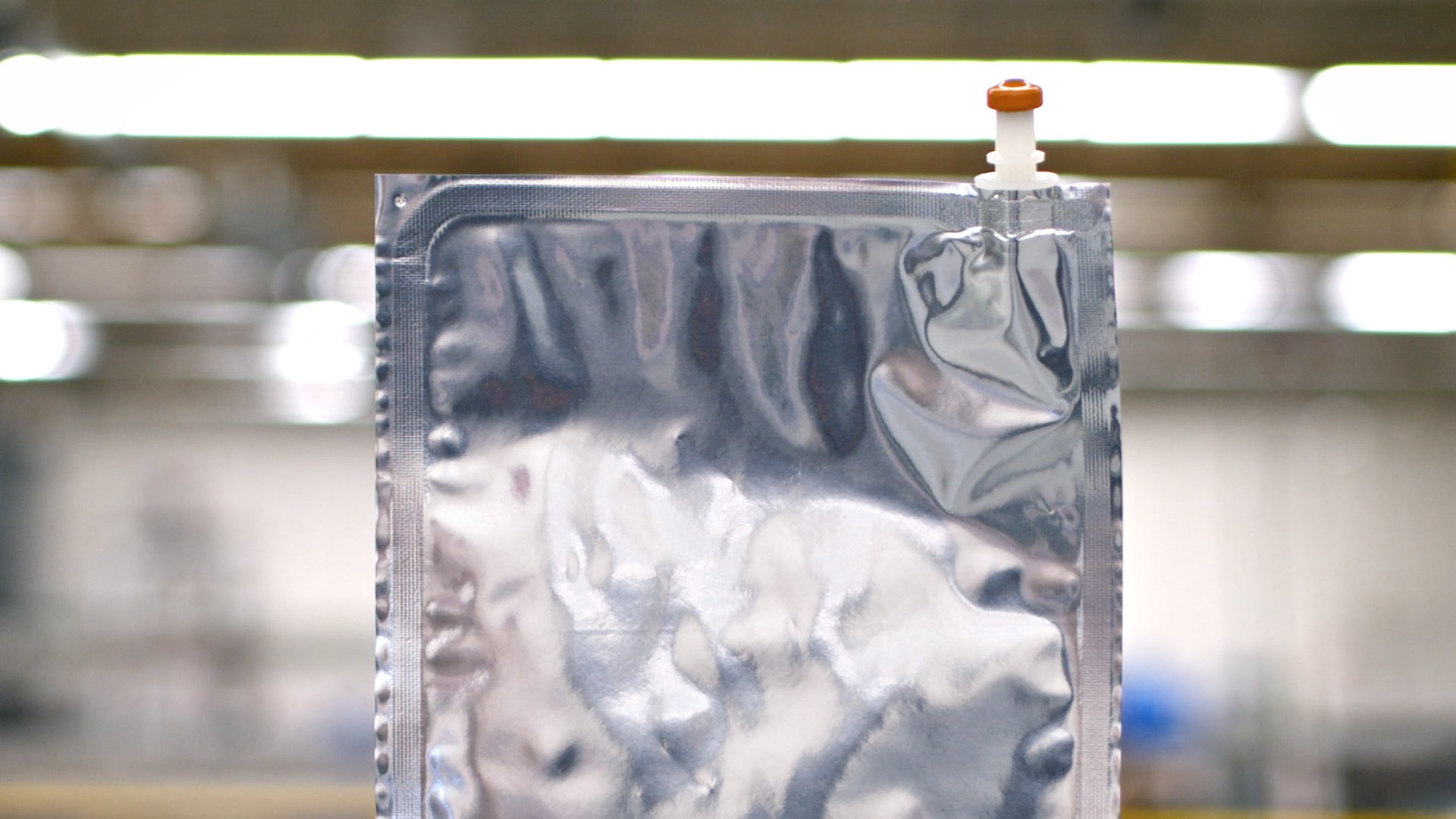
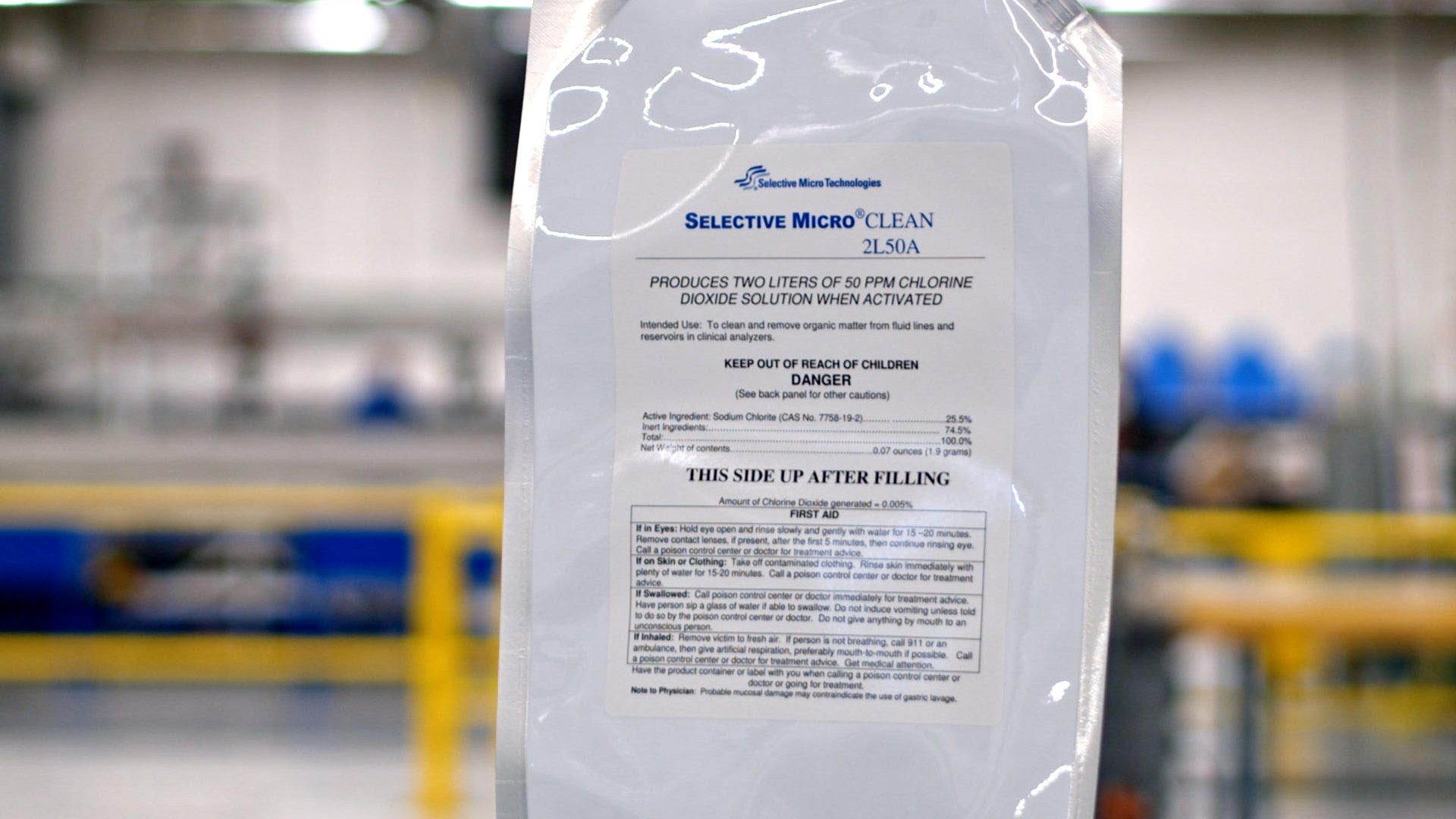
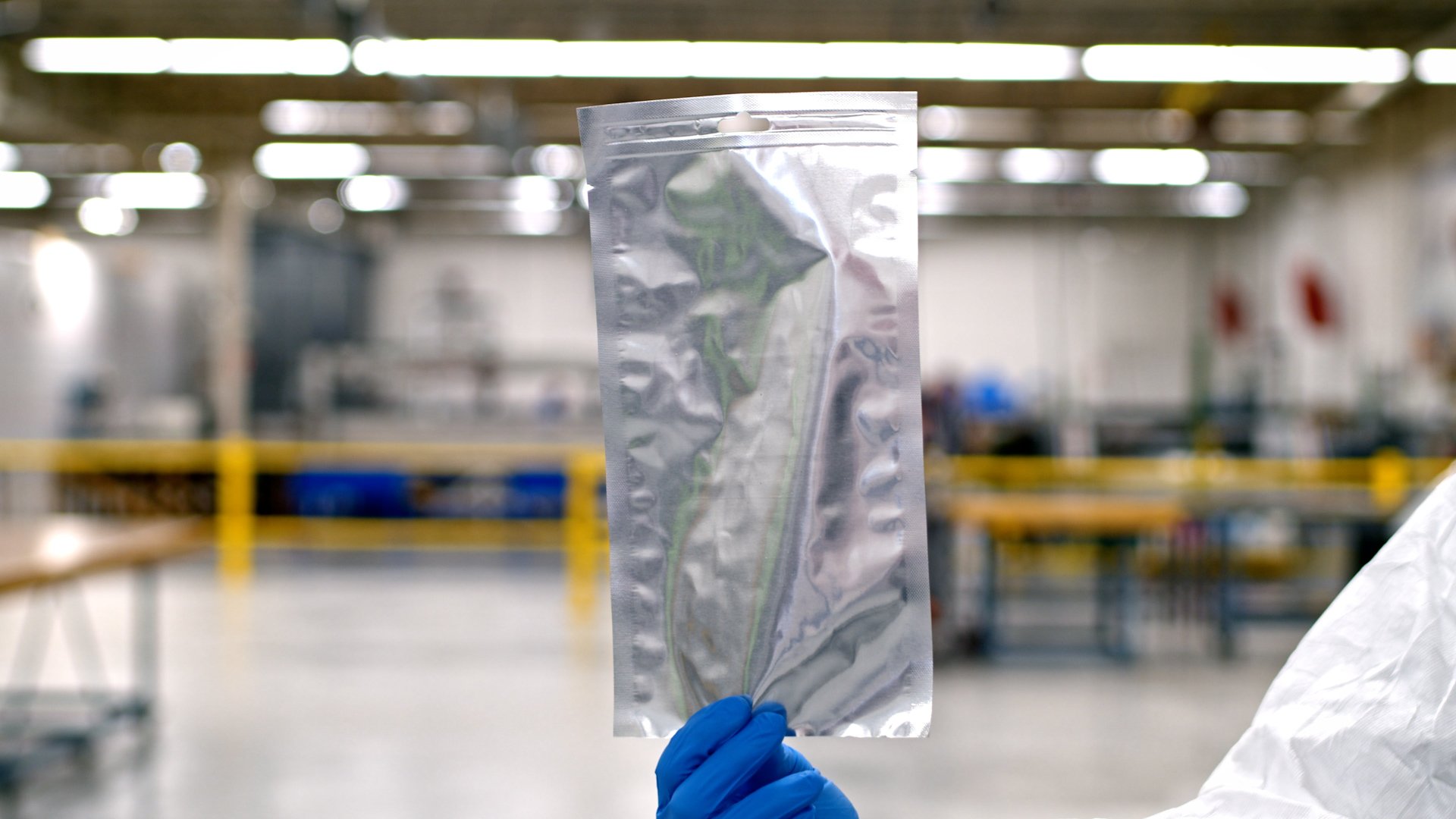
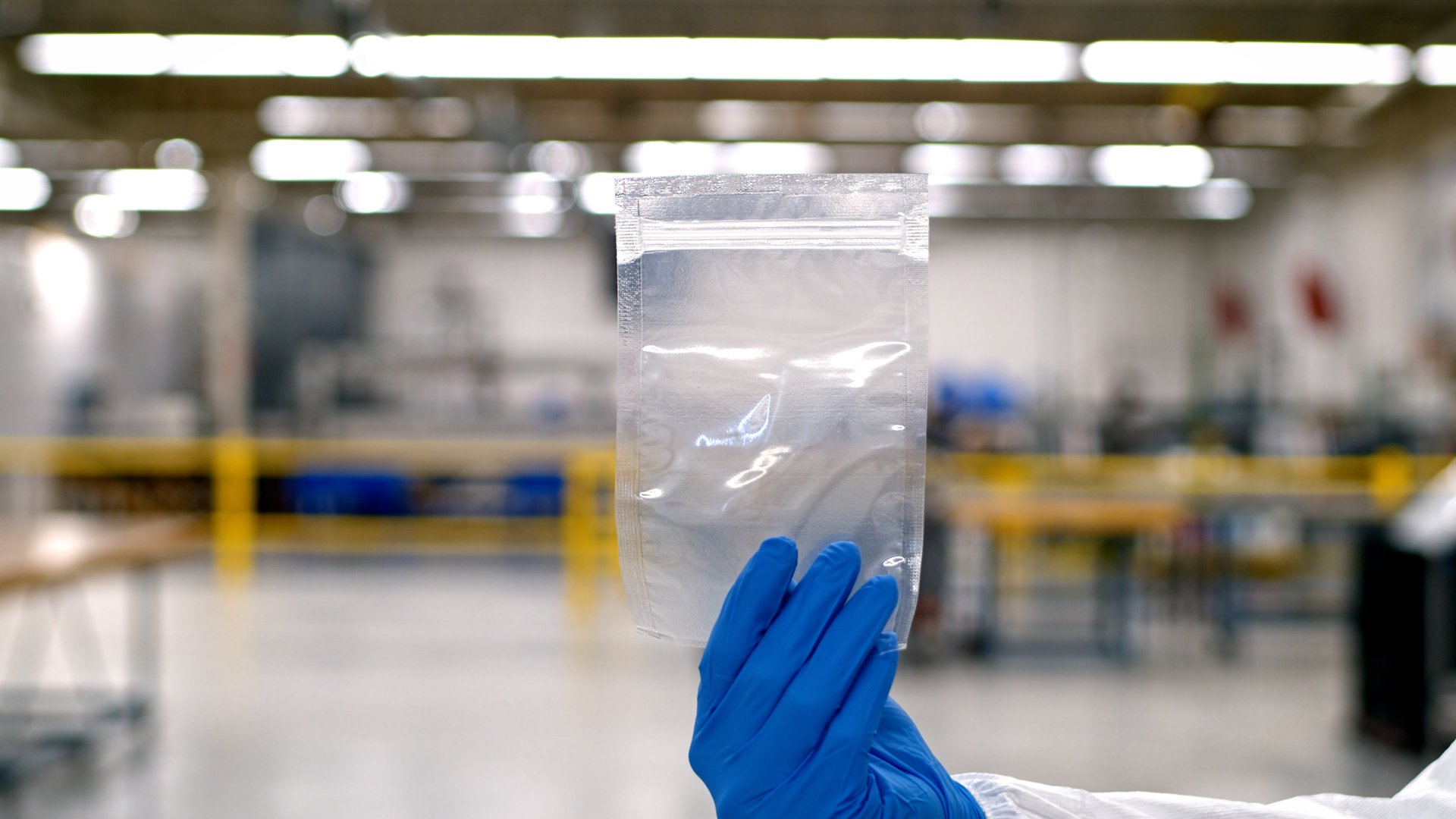
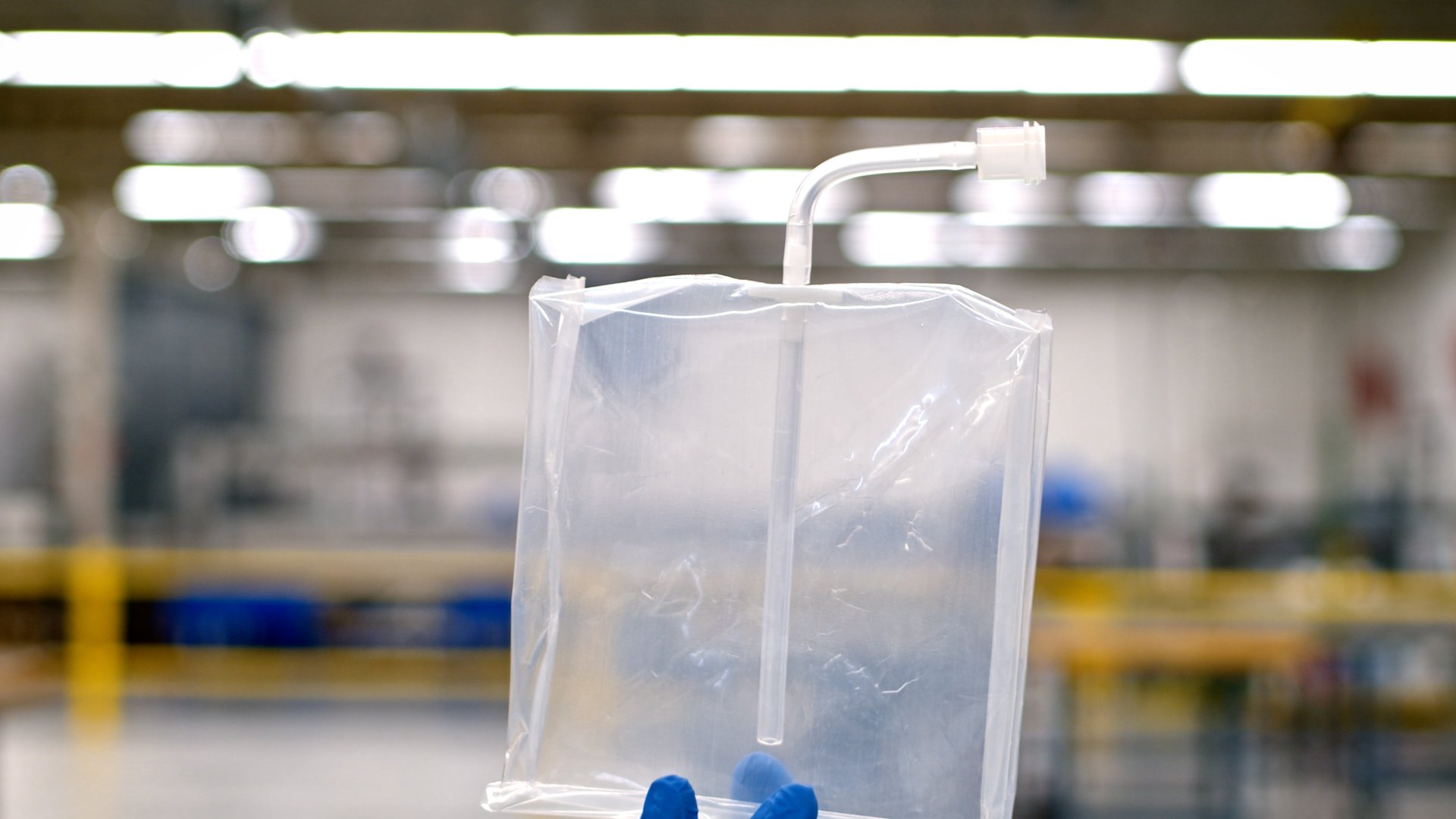
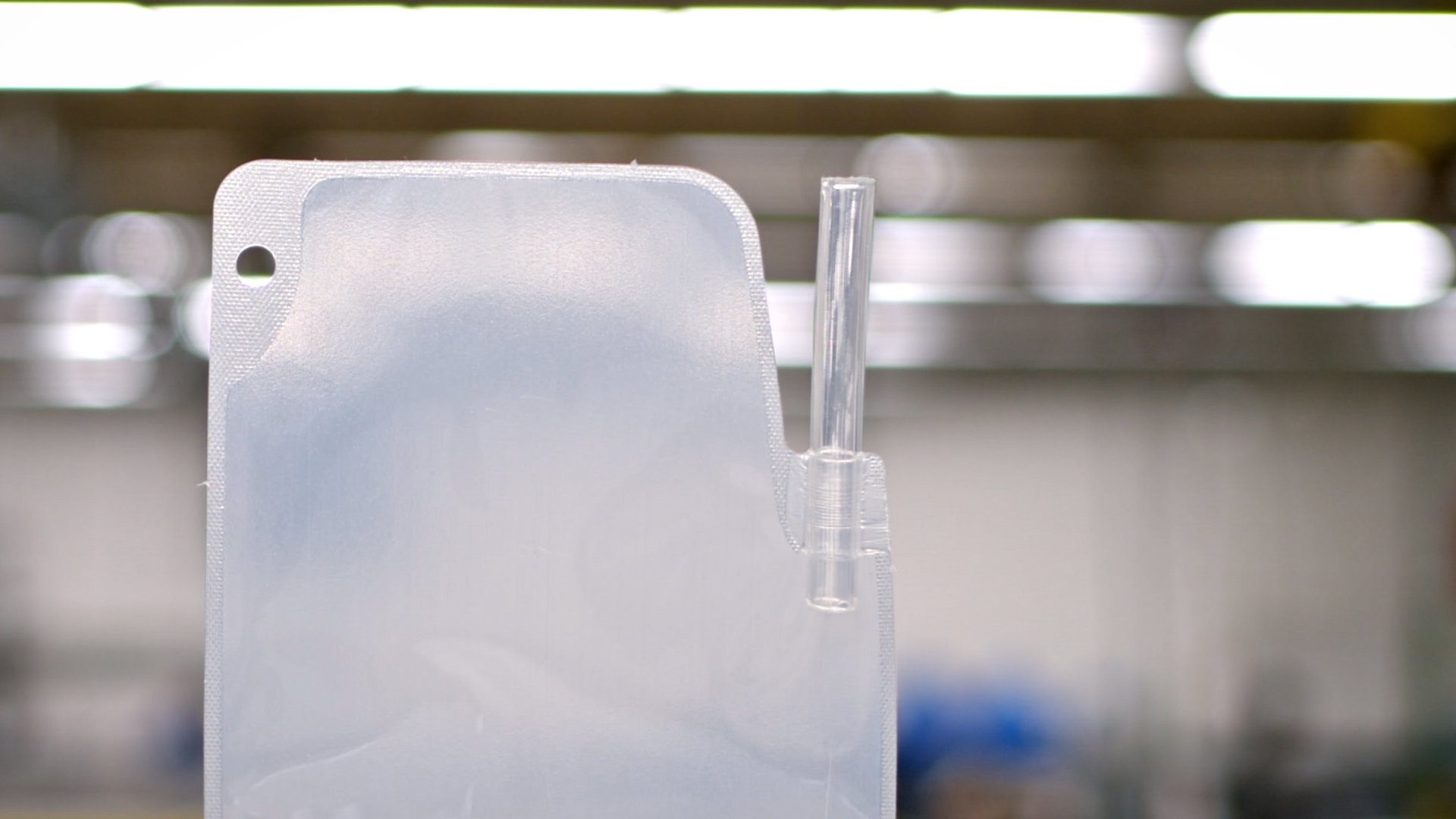
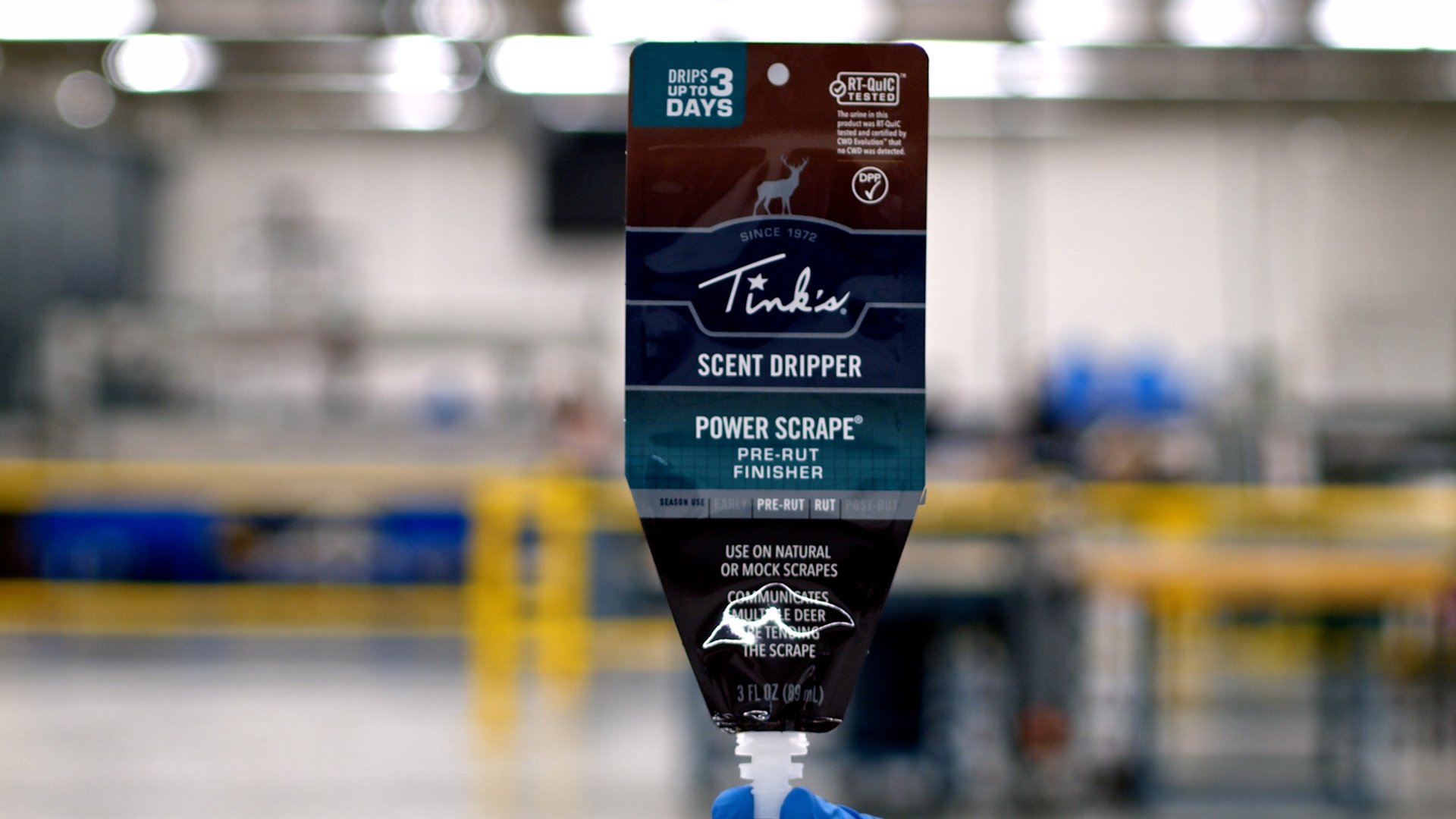
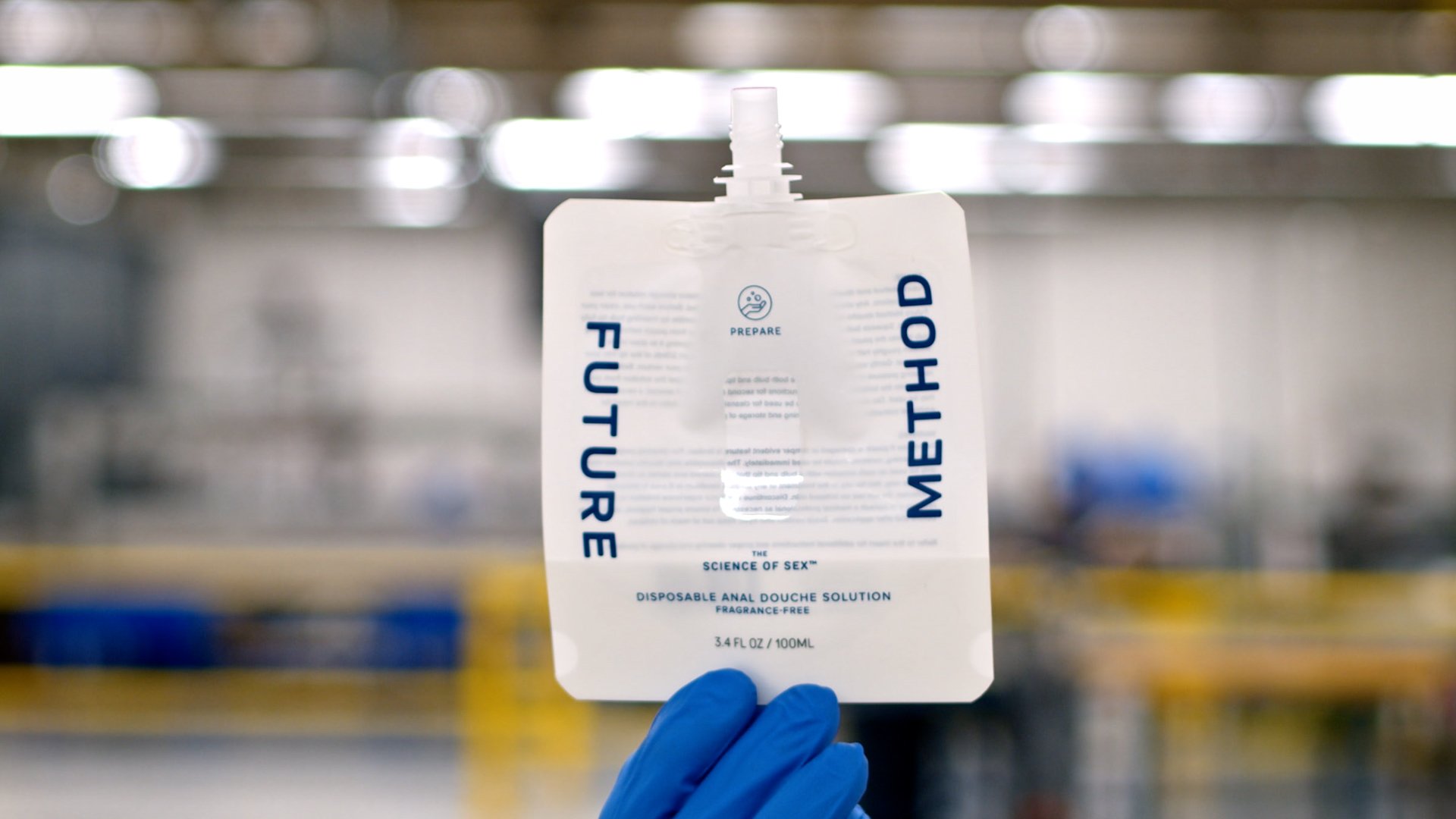
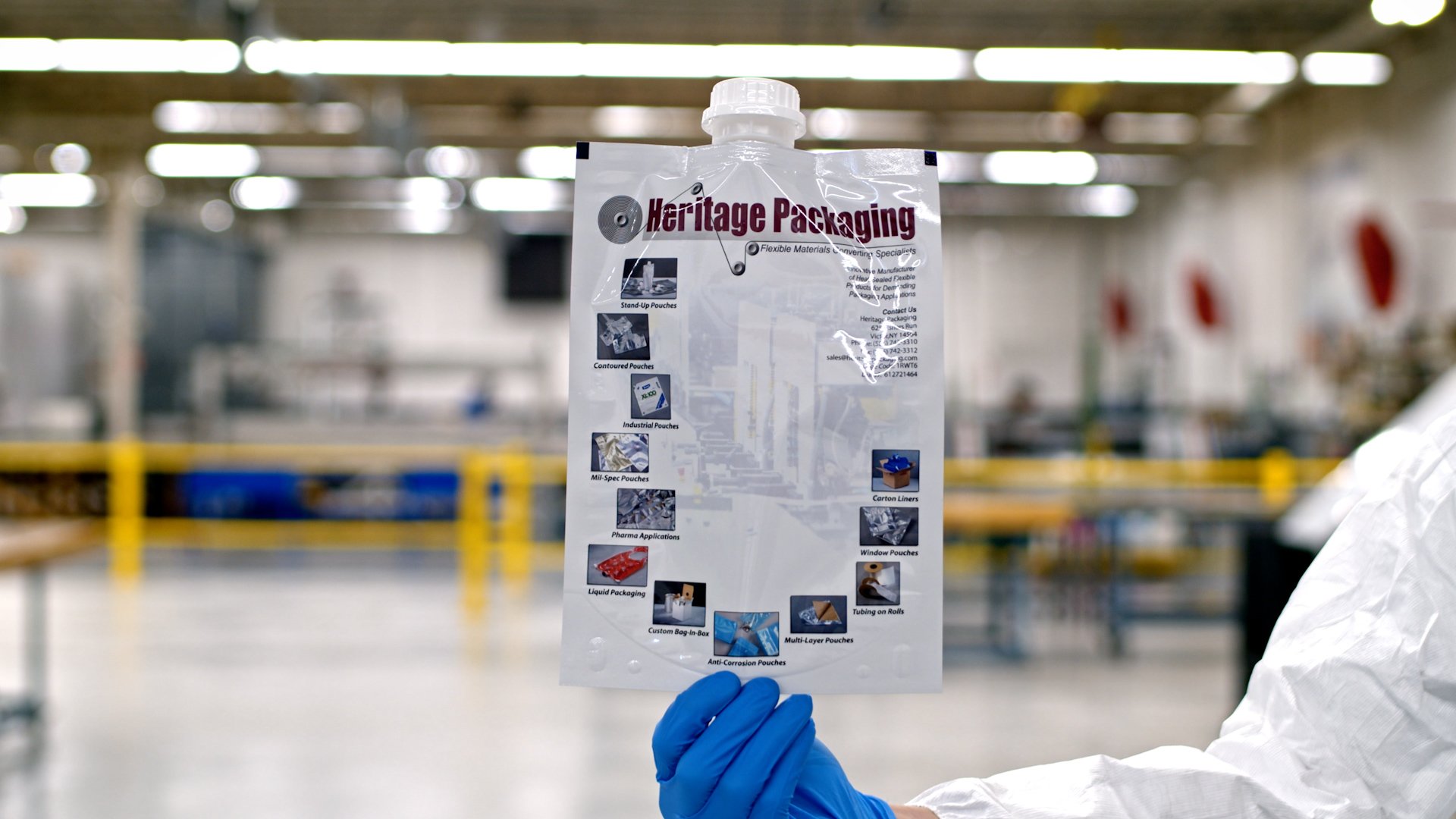
Off-Line Operations
Off-line operations are secondary operations that we perform either manually or with separate converting equipment, as opposed to directly on an automatic machine that also produces the product.
Holes & Punches
For example, we can add radiused cuts on the corners of a pouch, or a hole cut into one or two faces of film, or a hole into the seal using a punch.
Grommets
Once a hole is punched, we can add grommets, which reinforce the hole with metal or plastic crimps and prevent the packaging from breaking open when it’s hung or when another material is strung through the hole.
Grommets are beneficial for biomedical companies that need to hang heavy items like solution containers with reinforced hang holes.
Degassing Valves
We have the capability to add one-way valves which allow metered air or gas either into or out of an enclosure to help control the internal environment of an enclosure. Think of an at-home test kit that allows analysis of an individual's breath passed through the valve.
Die-Cutting
Our clicker presses, roll-through die cutters, and in-line hydraulic die-cutting presses use steel rule-cutting dies to cut the material into custom shapes up to 30” wide. This allows us to create products like form-fitting tank liners with circular bottoms for mixing operations.
We’re also able to produce short runs using our off-line equipment. This is a more economical choice for start-up orders or trial runs with quantities too small to justify a full pouch machine setup.
Capping
Capping is added onto a fitment in order to keep the contents inside. Many of our customers require custom caps like breather caps that let just some air out of the enclosure. We can put markers on caps to meter the flow of the contents and prevent the end user from opening it too much. We offer reclosable snap-on and screw-on caps that are compatible with either US or EU thread styles.
We can install crimp caps with rubber membranes (called septa) used for injectables to prevent spillage. When a needle pierces the septum, the membrane prevents any of the contents from escaping other than what is drawn through the needle.
Taping
Tape is used to either direct an end user or to help secure a closure. We can apply tamper-evident tape to specific locations of a finished product, or attach pressure-sensitive adhesive on an opening that an end user will then fold over and seal.
Labeling
Whether to warn end users of hazards or provide product information, we frequently add labels to finished products, using templates to ensure perfect placement. When necessary, we can also provide labeling inline on our automatic machines.
In-Line Operations
In-line operations are performed on our automatic pouch or liner machines during production as webs of material pass through the machines.
Custom Shaped Seals and Die Cutting
Our platen pouch machines are capable of heat sealing and then die-cutting material with custom-shaped seal tools and steel cut rule up to 18” wide. This allows us to produce bags, pouches, or liners in virtually any shape from roll stock to finished parts through the use of just one machine. Products with radiused corners, contoured shapes, tapers, or custom spouts are all produced using these machines.
Punched or Die Cut Holes & Shapes
Holes and contoured or angled shapes are offered as secondary operations, but we also have the capability to produce them in-line when it makes sense for the production process. Our machines can produce diagonal and/or radiused cuts to eliminate sharp corners and to install corner fitments. Additionally, our machines can make tear notches in “V”, “U”, and circular shapes.
Zippers
Our machines can install single and dual track zippers inline, providing a traditional positive closure method that is reclosable and allows easy access to the package contents for products ranging from PPE to simple medical devices.
Taping
Taping is done inline for applications that require directionality, like promoting a straight line from one tear notch to another. It is also used to reinforce a weak area in a bag, like around a punched hole in a pull tab.
Vision System
Our vision system Indicates the location of any particulate or embedded material defects within the bag above a certain threshold. This system assists us in meeting medical industry standards for particulate and foreign material.
Ports and Fitments
We install polyethylene or polypropylene-based ports, fitments, and spouts both inline and offline with openings that are from 4mm up to 6 inches. We produce hermetic seals around these items during installation, assuring product integrity and eliminating leakage.
We can provide one-way check valves with couplers to meter the flow of what comes into and out of a package. These are generally used in conjunction with the ports or fitments that we install.
We also install tubing directly into bags or pouches which can eliminate the need for a port or fitment in some applications.
Kitting
Some customers need several pieces put together in a kit. We frequently take our finished packaging products and kit them together with items like desiccants, oxygen scavengers, humidity indicator cards, multiple configurations of pouches, hardware items, and other customer-specific apparatus.
Cleaning, Sanitizing, Sterilizing
Our plant is certified in SQF Food Safety Code for Food Packaging, Edition 9, a comprehensive global food safety program. While SQF stands for Safe Quality Food, we find that many customers in the biomedical industries approve of the level of cleanliness we maintain on a daily basis.
When requested we work with our trusted domestic vendors to sanitize our finished products by cleaning them in an appropriately rated clean room to specified cleanliness standards.
We can also arrange for product sterilization through irradiation in accordance with customer specifications.
Printing and Labeling
In-house, we can imprint directly on your packaging product in a 4” x 5” area. One-color printing in green, red, blue, and black is available and is frequently used to print date/lot numbers. We can also print one-color labels with custom content in-house that are used either on the parts themselves or the boxes they are packed in.
We also maintain strong relationships with suppliers who can print material in full color using digital printing, as well as flexo and gravure printing. So while a lot of our packaging products are manufactured with high-performing materials that are plain looking, we also produce pouches and bags with printed material that would catch a consumer's eye.
Testing
Our quality management system is based on MIL-STD-1916 and includes GMP & SQF protocols. All of our made-to-order products receive quality inspections and instrument testing. Our lab houses numerous testing instruments and methods for data entry.
Our quality control team moves about the building constantly during the day, performing checks and tests to ensure all quality standards are met. Additional testing, like drop testing or boil testing, is available upon request.
Inhouse we have:
Burst strength testing equipment
Tests the strength of seals as a whole, and finds any points of weakness in the bag.
Tensile testing equipment
Tests a 1” section of a seal by pulling it apart to see if the seal strength matches what the film manufacturer or customer specifies.
Leak/pressure decay testing equipment
Vacuum Chamber (immersion) testing equipment
Similar to burst strength testing, but is a quicker visual inspection method.
Mil-Spec hang test equipment
We can arrange for ISTA/ASTM testing.
Conclusion
We hope you enjoyed a closer look at many of the special features and secondary operations that we can provide when customizing our pouches, liners, bags, covers, and other enclosures for the biomedical industries.
If you’d like to talk to our team about a packaging solution for your specific application, send us an email or give us a call to see if an engineered flexible packaging solution is right for you.
And If you want to know more about what we do at Heritage Packaging, be sure to sign up for our newsletter on our website for more free resources and answers to frequently asked questions.